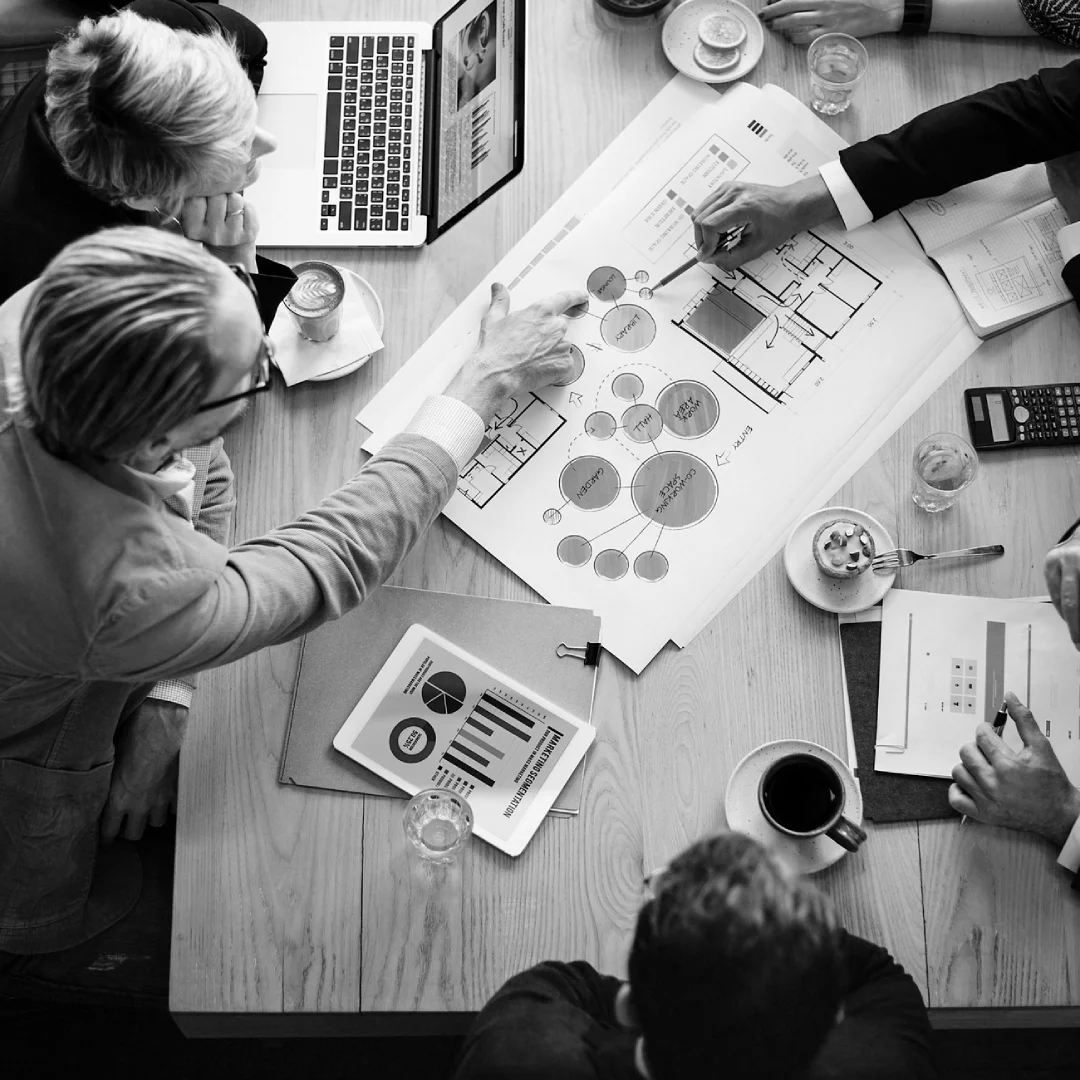
Step 1. Design Concept
We align business objectives with technical realities, ensuring each project begins with a solid foundation grounded in thorough analysis and structured planning.
- Define client objectives and operational scope
- Prepare project-specific questionnaires for data collection
- Conduct comprehensive mapping of existing facilities
- Specify product requirements (chemical and physical properties)
- Analyze raw material supply, including chemical composition and availability
- Evaluate environmental conditions and permitting requirements
- Outline HR requirements for future operational phases
- Integrate market dynamics and logistics analysis
- Establish system conditions, constraints, and interdependencies
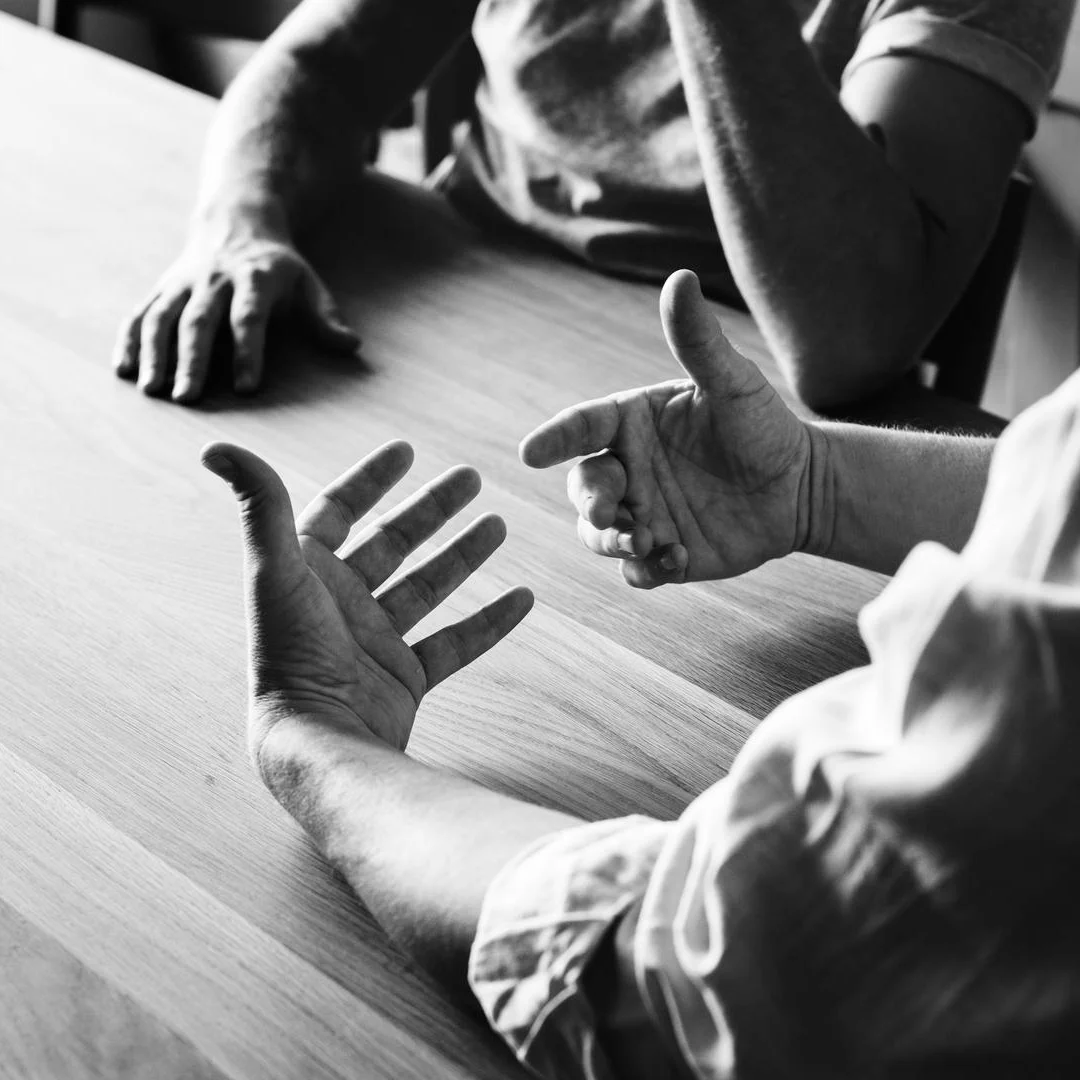
Step 2. Project Definition
We transform initial concepts into actionable plans through layout design, technology selection, and feasibility evaluations tailored to the project’s unique requirements.
- Develop process flow diagrams and layout options
- Describe key process steps with performance and operational data
- Select core technologies for each production stage
- Calculate production capacity and emissions levels and define interface point
- Define safety systems, utility needs, and auxiliary services
- Plan logistics, material flows, and handling equipment (cranes, vehicles, etc.)
- Prepare CAPEX capital cost estimates and validate site conditions
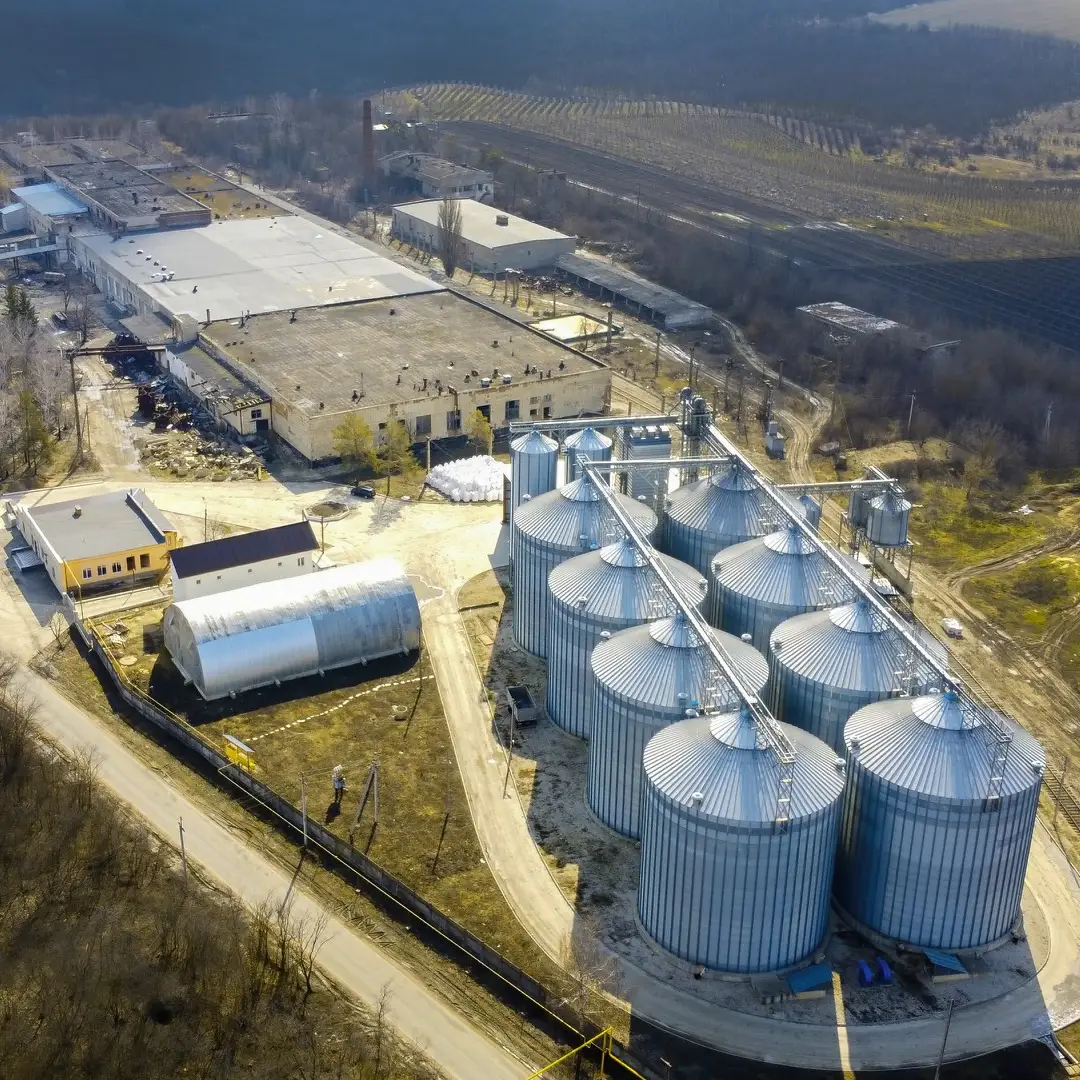
Step 3. Supplier Selection
We ensure optimal procurement decisions by identifying and engaging suppliers with the technical capabilities and commercial strength aligned to project goals.
- Define inquiry packages, technical specifications, and design assumptions
- Prepare clear tender instructions and milestone schedules for bidders
- Manage technical clarifications and bid harmonization(technical & commercial merit)
- Evaluate bids based on technical compliance and commercial value
- Recommend qualified vendors through structured comparisons
- Support final contract negotiations and supplier onboarding
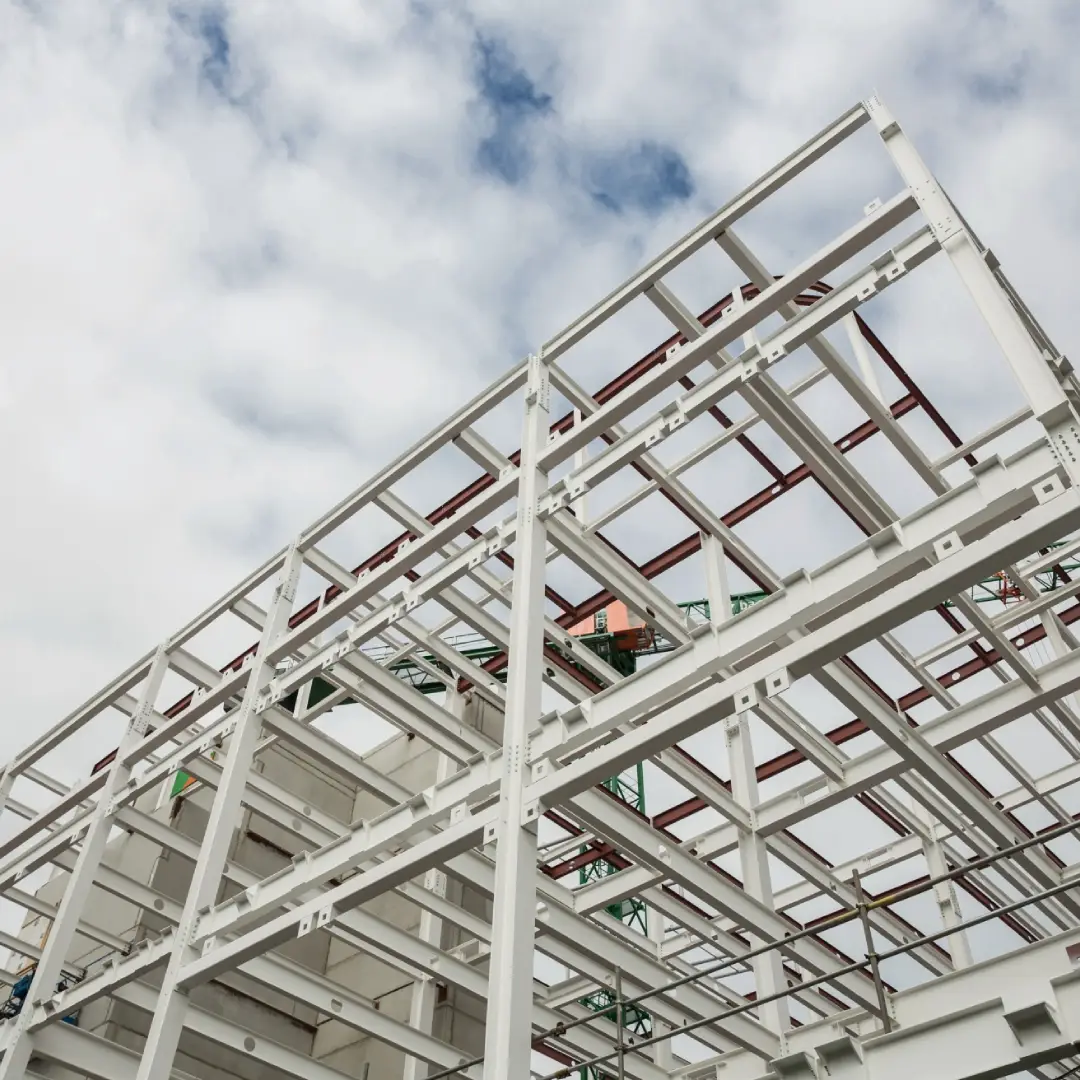
Step 4. Project Realization & Management
We oversee the execution phase to maintain quality, control costs, and ensure timely delivery — from engineering through construction and testing.
- Perform detailed engineering reviews and documentation checks
- Provide project management and cost control support
- Evaluate site logistics and plant layout efficiency
- Supervise procurement, fabrication, and inspection activities
- Manage change processes and monitor construction progress
- Oversee commissioning readiness and performance validation
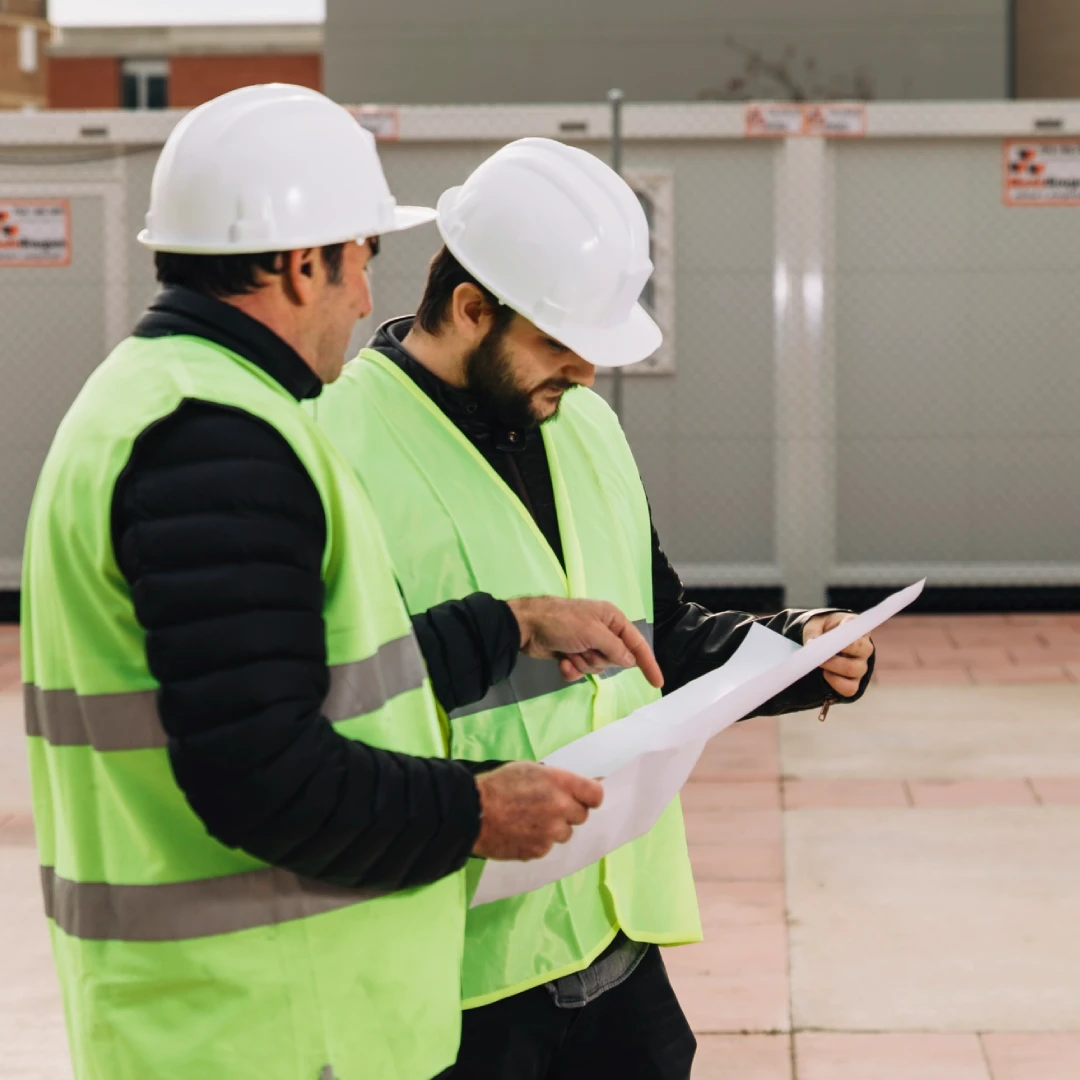
Step 5. Commissioning & Start-up
We ensure a seamless transition from construction to operations by guiding staff, verifying system functionality, and embedding operational knowledge.
- Oversee construction completion, supervise commissioning and early-stage operations)
- Train operations and maintenance personnel
- Review manning schedules and define requirements for key personnel
- Oversee system start-up and performance testing
- Transfer operating documentation and procedures
- Develop tailored maintenance and reliability programs
- Provision of operational know-how, coordinate with technology suppliers for integrated knowledge transfer
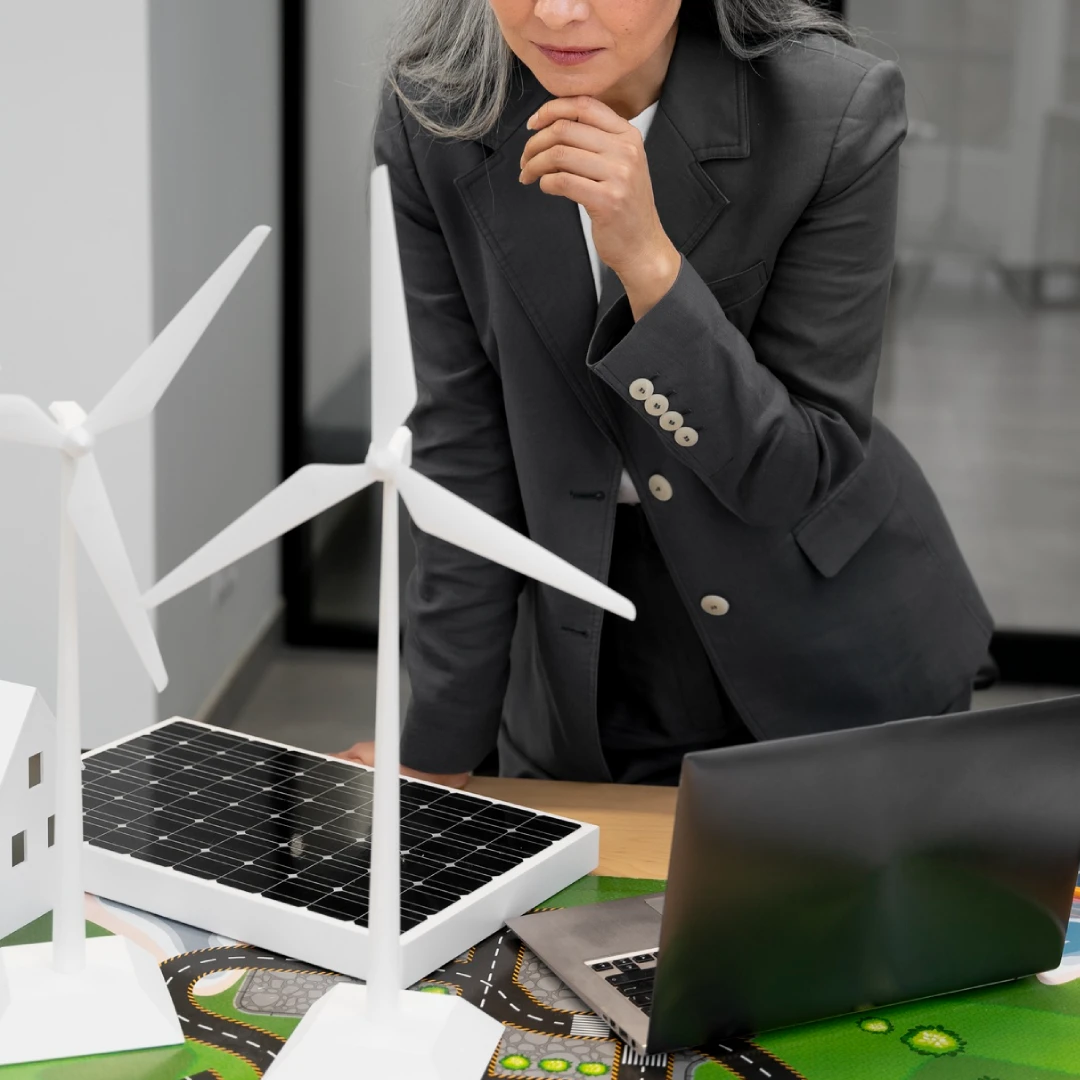
Step 6. Operational Assistance
Supports sustained performance through real-time evaluation, ongoing training, and strategic improvements tailored to evolving process needs.
- Evaluate process performance and cost efficiency
- Simulate and model improvements using real-time data
- Propose and implement improvement strategies
- Deliver on-site training and process optimization programs
- Provide ongoing management and technical assistance